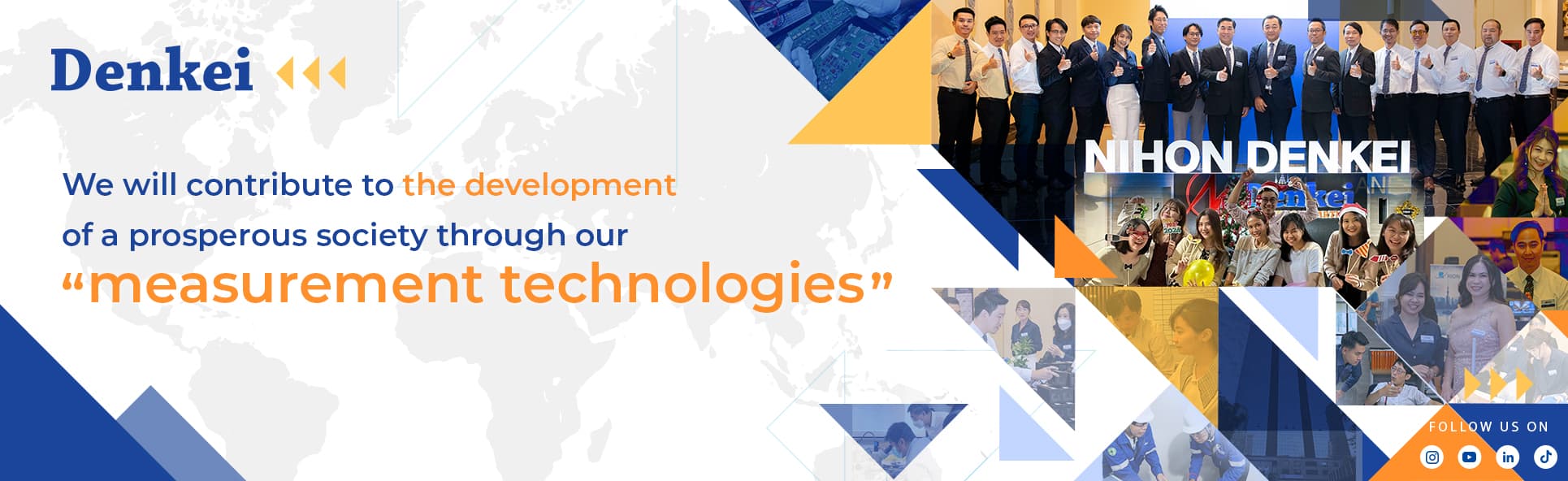
This is Kiyono from Nippon Denkei (Thailand).
In addition to the trend of shifting production bases to Southeast Asia, the importance of automation in Thailand and other Southeast Asian countries is expected to increase in the future due to the recent impact of the COVID pandemic. Here, we would like to introduce JUKI (which provides industrial equipment and systems)’s inspection and measurement automation solution and parts management automation solution, together with Mr. Shinpei Yamashita of JUKI SMT ASIA CO., LTD.
Visual inspection measuring machine SE1000(left) Hybrid inspection machine HE1000(right)
"Our inspection and measurement instruments were originally developed for SONY as inspection instruments that could be used at circuit board mounting sites. The fusion of the image processing and inspection technologies that have been used for quality control of many SONY products such as smartphones, cameras, and TVs, and the mechatronics technologies cultivated through the manufacture of JUKI industrial sewing machines, has expanded business opportunities in a variety of inspection fields other than mounting circuit board inspection.
Recently, the need for automation has been increasing in various inspection sites due to clients' increased requirements for sophisticated inspection and quality control," says JUKI's Mr. Yamashita.
JUKI's inspection and measuring equipment is equipped with material handling system for transportation, and its advantage is that it can complete the automation of visual inspection and measurement in a single unit. If implemented it into a process where manual inspection using measuring tools or visual inspection is performed, significant automation and effective use of resources can be expected.
Example of benefits of product implementation
1. Quantify sensory inspections that rely on human intuition and experience
2. Reduction of labor cost and outflow cost by 100% inspection and shortening inspection time
3. Automation and visualization of the entire inspection process and realization of a stable inspection system
4. Improved traceability and data reliability
Implementation track record in a wide range of fields
Automobile and motorcycle parts, electronic parts, processing tools and parts, cosmetics, etc.
Large-capacity general-purpose model ISM 3600
"The ISM series was developed to automate the labor-intensive management of electronic components.
Not only in Thailand, but also worldwide, 90% of electronic circuit board production factories are loading/unloading and managing components manually.
Manual work causes troubles and issues such as followings
✓ Cannot locate the part you are looking for and takes a long time to find it
✓ Workers are overloaded and cannot rest
✓ Humidity control is required, but not possible
✓ Parts dispatch error has made the trouble to be twice as much
✓ Management has become complicated due to an increase in the number of parts types, and we want to make a database of parts management
The ISM series solves these problems.
We have already sold more than 1000 units worldwide, mainly in the automobile and EMS industries, and we believe that we will be able to further meet the needs for automation of parts management in the future." (Yamashita of JUKI)
Features of the ISM series
1.System linkage
Data linkage and FIFO reduce work-in-process and improve efficiency of ordering operation
2.Case compatibility
Use of an electrostatic case that can accommodate a variety of supply styles.
3.Space saving
70% reduction in space with large capacity storage
4.Humidity control
Controls products at low humidity and has a humidity traceability function.
5.Automatic warehousing/delivery
No operator required during warehousing/ delivery
Head Office
Tel: +66(0)2-675-5688
Yoshino
Mobile: +66(0)88-974-0813
Email: yoshino@n-denkei.co.th
Saji
Mobile: +66(0)96-286-1601
Email: saji@n-denkei.co.th
Laem Chabang sales office
Tel: +66(0)3849-5186~7